Blog
Preventing Food Recalls
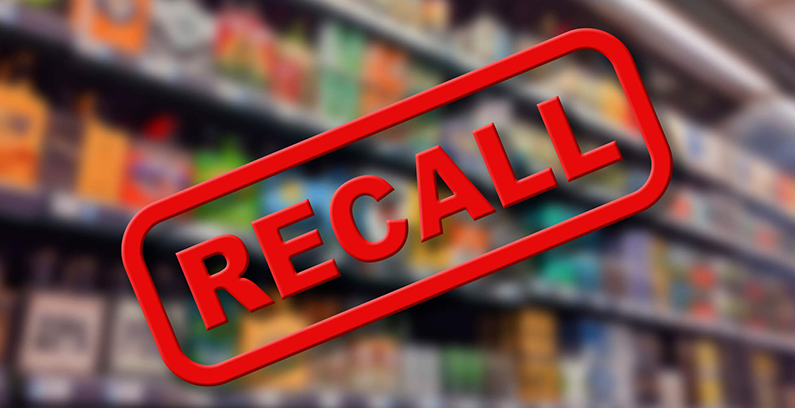
An article in Food Safety Tech by Jeff Clinton, What Food Manufacturers Can Learn from the Baby Formula Recall, discusses costly lessons learned from recent food recalls. Among the recommendations are having a robust sanitation program and empowering employees. One of the best ways to accomplish these recommendations is to establish and validate an environmental monitoring program using indicators. Some of which can give results in real-time.
Validate Environmental Monitoring
Proper remediation of positive locations and additional surveillance samples surrounding the positive, called vectoring, are ways of reducing the risk of pathogen contamination in food production zones. For example, Adenosine Tri-Phosphate (ATP) and aerobic counts are good indicators of Listeria risk. Whereas ATP and Enterobacteriaceae (EB) bacteria are good indicators of Salmonella risk. ATP testing provides real-time results to sanitation and production personnel, allowing immediate cleaning as remediation before food contact or processing. Environmental monitoring for bacterial indicators provides a food plant with quick 24-hour results that acts as a report card on how the ongoing sanitation program is working. Quality personnel may adjust procedures to testing locations to focus on problematic areas, including zone, surrounding areas, and products needing more attention.
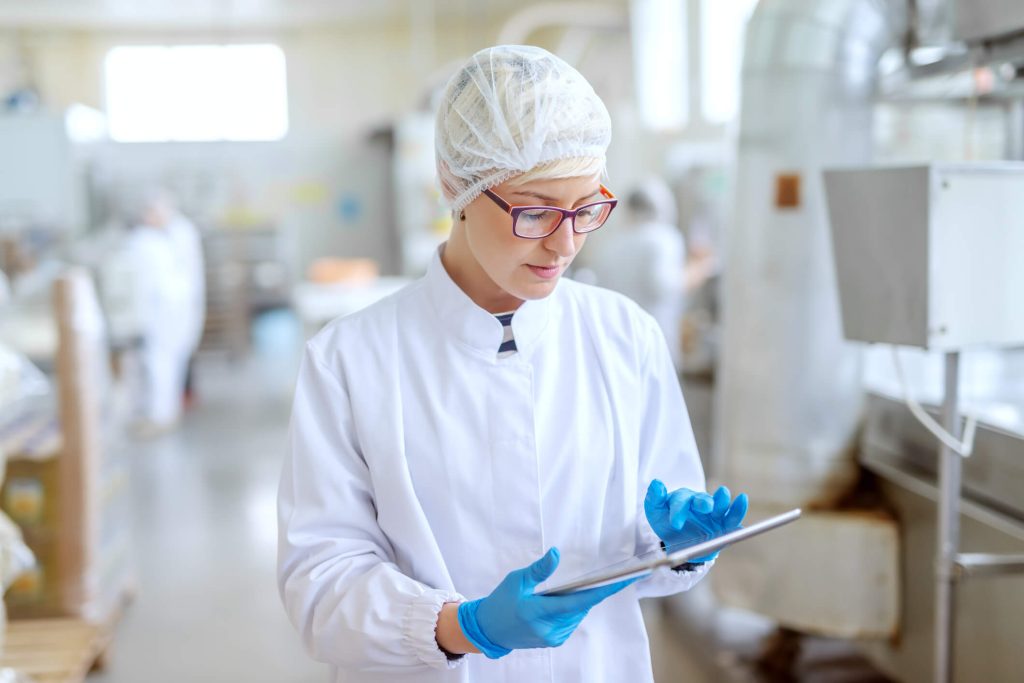
Importance of Indicator Tests
In past decades, criticisms of using indicator tests were that they are not sensitive enough, nor specific, to detect pathogens at the low levels tolerated in finished foods or raw materials, which is at the single colony-forming unit CFU/25 gram or 100 gram or 375-gram food. However, manufacturers have learned that indicators are very effective because they are the first simple and fast checks indicative of potential process control breakdown. Indicators are like a micro alarm verifying sanitation processes are working. With repeated testing, remediation, and vectoring in zones surrounding the primary production zone, the higher-risk areas for pathogens are identified and reduced. There is also a great benefit in programs like these for improving and extending product shelf-life.
Because indicator tests are not as sensitive as pathogen tests, it makes sense that environmental tests and raw material tests be as sensitive as possible. This is particularly true for critical food production, like infant formula, intended for consumers with immature or compromised immune systems. A plant manager at an infant formula plant can rest easier knowing that their EB test is detecting 1CFU/5 mL from an environmental swab in their critical zones, which is five times more sensitive than the normal practice of 1CFU/1 mL of swab broth. This high-sensitivity test provides five times the cleaning verification of sanitation programs and improvement from standard practices. Likewise, a food plant can use higher sensitivity indicator tests with incoming raw material testing. For example, an infant formula plant can verify less than 1 CFU EB per gram of milk powder using two high-sensitivity tests as opposed to the standard practice of 10 CFU EB per gram.
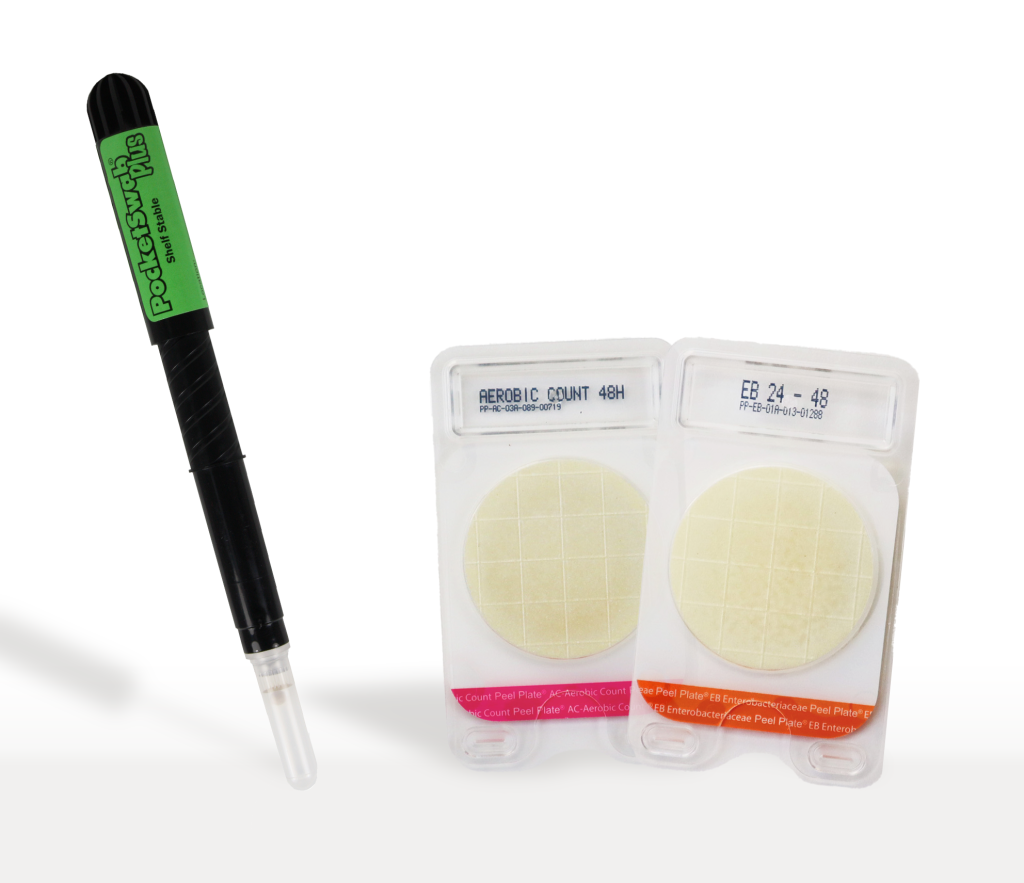
Turn to Charm Sciences for Verifying Food Safety Practices
Charm Sciences is a manufacturer and supplier of ATP sanitation and microbial indicator tests to the food industry. We offer a variety of real-time, high-sensitivity ATP indicator tests for water and also for allergen cleaning verification. We make 5 mL volume microbial tests for Enterobacteriaceae, coliform, E. coli, and yeast and mold. Charm is also a partner to the food industry providing testing services and working with our stakeholders to develop sanitation and raw material testing protocols that address the industry’s hazards and risk assessments.
The lessons learned from food recalls are reminders that food production plants must maintain their due diligence in training personnel and empower them to do corrections and remediations in their daily production routines. Equipping plant personnel with Charm Sciences’ tools provides a solid foundation to reduce food safety risks which is the goal of all quality programs.
About Charm Sciences
Established in 1978 in Greater Boston, Charm Sciences helps protect consumers, manufacturers, and global brands from a variety of issues through the development of food safety, water quality, and environmental diagnostics tests and equipment. Selling directly and through its network of distributors, Charm’s products serve the dairy, feed and grain, food and beverage, water, healthcare, environmental, and industrial markets in more than 100 countries around the globe.